Automatic conical pail production line
1.WHAT IS A CONICAL PAIL?
It is made of three pieces of metal sheet (mostly tinplate), the body, the bottom and the lid of the Cans. The cans is conical. The tank body has two ribs, Range of drums: capacity 10-25l, diameter 200-300mm, height 150-480mm.
2.WORKING PROCESSOF AUTOMATIC CONICAL PAIL PRODUCTION LINE
The production line is suitable for the automatic production of 10 liters to 25 liters’conical pail. total power: approx.130KW,total floor space: 250㎡ .total length:approx.36 meters. total manpower: 3-4 people. Production capacity: 28-30cpm. Pail height range: 170-460mm.Pail diameter range:200-300mm
Technical flow: cutting the tin sheet to blank-rounding-welding-inner and outer coating (inner powder coating and outer coating)-drying-cooling conveying-conical expanding-flanging-curling-beading-bottom lid feeding-seaming-turning over-ear lug welding&coating&meal handle assembly-leak testing-packaging
First place the cut can body materials into the automatic resistance welding machine’s feeding table, Suck by the vacuum suckers,send the tin blanks to the feeding roller one by one.through the feeding roller, the single tin blank is fed to the rounding roller to conduct rounding process, then it will be fed to the rounding forming mechanism to make rounding.The body is fed into the resistance welding machine and make welding after the accurate positioning. After welding, the can body is automatically fed into the rotary magnetic conveyor of the coating machine for outer coating, inner coating or inner powder coating, Which depends on customer’s various need.It is mainly used to prevent the side welding seam line from being exposed in air and rusting.The can body should be placed in induction drying oven to dry if it’s inner coating or inner powder coating.Afer drying, It will be fed to cooling device to make natural cooling.The cooled can body is then fed to the conical pail combination machine, and the can body is in an upright state going through the uprighting conveyor.The first operation is the can body conical expansion. When the can body is in position, on the can body lifting tray which is controlled by a servo motor, and the can body is sent by this lifting tray to the conical expanding mold to make conical expanding.The step 2 is pre-flanging The step 3 is curling.The upper mold is fixed on the machine body, and the lower mold, which is mounted on the CAM, completes the flanging and curling when the CAM is jacked up.The step 4 is beading. After completing the above four steps,When the bottom lid auto feeder detects the can body coming, It will automatically feed one bottom lid to the top of the can body,and then both the can body and the bottom lid will be clamped to seaming machine head to make auto seaming.After bottom seaming, it is fed to automatic double spots ear lug welding machine,through automatic side welding seam indexing, Cam conveyor conveying, mechanic paint breaking, also equipped with automatic ear lugs vibrating discs,finish accurate welding task on conical pail.Then,The pail is fed to handle making and assembly station to finish automatic handle assembly.Lastly, The finished can is conveyed to the automatic leak testing station by conveyor.Through the accurate air source detecting step, The unqualified products will be tested and fed to the fix area.The qualified pails will come to the packing table for the final packaging.
3. CONICAL PAIL AUTOMATIC PRODUCTION LINE EOUIPMENT COMPOSITION:
Single gang slitter

Single gang slitter | |
Maximum size of cutting material (L*W) | 1100*1100mm |
Minimum size of cutting material (L*W) | 200*400mm |
The fastest speed | 50 sheets/min |
Power supply | 380v/50HZ |
Total power | 3.5kw |
Device Weight | 1800kg |
Feed rack load capacity | 3T |
General Can Body Welder

General Can Body Welder | |
Welding frequency | 100-280Hz |
Welding speed | 8m-15m/min |
Production capacity | 25-35cans/min |
Can body diameter | Φ220mm-Φ300mm |
Can height | 220mm-500mm |
Adapt to tinplate thickness | 0.2mm-0.4mm |
Copper wire diameter | Φ1.5mm-Φ1.8mm |
Weld seam amount | 0.6mm-1.0mm |
Power supply | 380v 50Hz Three-phase power |
Installed power | 20KW |
Cooling water | >0.4MPa,12-20℃,40L/min |
Air consumption | ≥200L/min>0.5Mpa |
Device Weight | About 3000KG |
Dimensions(L*W*H) | 2200mm*1520mm*1980mm |
Inside Side Stripe Power Coating Machine

Inside Side Stripe Power Coating Machine | |
Applicable can diameter | Φ52mm-Φ350mm |
Transfer speed | 10-20m/min/20-60/min |
Coating width | 6-14mm |
Powder material | Polyester Epoxies |
Installed power | 2.5KW |
Air consumption | ≥300L/min>0.5Mpa |
Input power | AC 220v,50HZ |
Device Weight | 500KG |
Dimensions(L*W*H) | 900*900*2200mm |
External Spray Conveying Machine

External Spray Conveying Machine | |
Applicable can diameter | Φ52Mmm-Φ350mm |
Applicable can height | 50mm-600mm |
Coating speed | 8-16m/min/25-50m/min |
outside Coating width | 8-18mm |
Compressed airm | 0.4MPA/cm² |
Input power | ≥380v/50HZ |
Dimensions(L*W*H) | 1800*600*1300mm |
Device Weight | 500KG |
Induction Oven
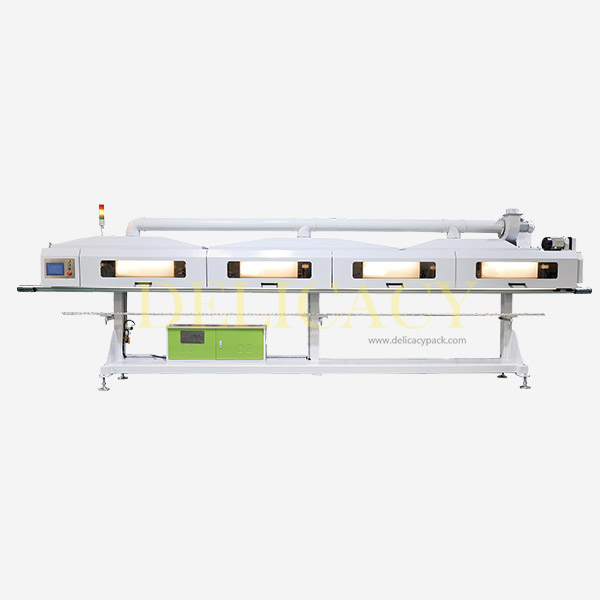
Induction Oven | |
Burner power | 1-2KW |
Burner heating speed | 4m-7m/min |
Suitable small can diameter | Φ45mm-Φ176mm |
Suitable big can diameter | Φ176mm-Φ350mm |
Can height | 45mm-600mm |
Cooling water | >0.4MPa,12-20℃,40L/min |
Air consumption | ≥50L/min>0.5Mpa |
Full automatic can body combination machine

Full automatic can body combination machine | |
production capacity | 25-30cpm |
drum body diameter range | Φ200-300mm |
drum body height range | 170-460mm |
thickness | ≤0.4mm |
total power | 44.41KW |
pneumatic system pressure: | 0.3-0.5Mpa |
body uprighting conveyor size | 4260*340*1000mm |
combination machine size | 3800*1770*3200mm |
electric carbinet size | 700*450*1700mm |
combination machine weight | 9T |
Automatic can sealing machine

GT4B30 Automatic can sealing machine | |
production capacity | 25-30cpm |
diameter range | Φ200-300mm |
height range | 170-460mm |
thickness | ≤0.4mm |
total power | 4.55KW |
pneumatic system pressure: | >0.3-0.5Mpa |
the front section conveyor’s size | 2780*310*750mm |
seaming machine size | 1350*1290*1980mm |
electric carbinet size | 600*350*1400mm |
outfeed conveyor size | 2000*340*760mm |
seaming machine weight | 3T |
Blue Bucket Medium Frequency Welding Spray Handle Equipment

Blue Bucket Medium Frequency Welding Spray Handle Equipment | |
Range of can bodies | Blue bucket |
Range of can height | 220-480mm |
Capacity per minute | Up to 30pcs/min |
Power required | 30KW |
Dimensions of Principle Machine(L*W*H) | 3900*2800*2360mm |
Dimensions of Unreeling Machine(L*W*H) | 1030*1030*1530mm |
Principle Machine Weight | 5000KG |
Unreeling Machine Weight | 500KG |
Lubrication system | Manual lubrication |
Height of input station | 840-1000mm |
Compressed air required | 0.4Mpa*10L/min |
Leak tester

Leak tester | |
Detected product volume range | 18-20L |
Equipment air pressure | 4-6Bar |
Check pressure | 10-15Kpa |
Detection accuracy | 0.17mm |
Detection speed | 35PCS/mins |
Device Weight | 3800KG |
Dimensions(L*W*H) | 3400mm*2200mm*2300mm |
Input power | 380v/50HZ |
THE LAYOUT OF THE PRODUCTION LINE
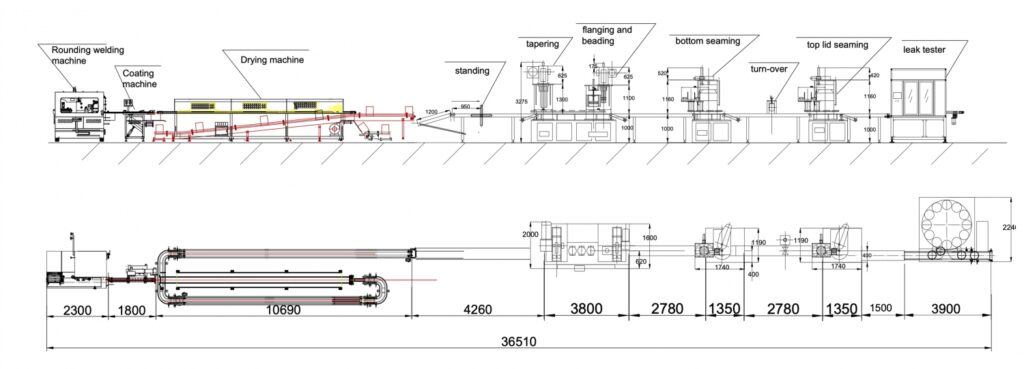
TIN CAN MAKING ARTCRAFT
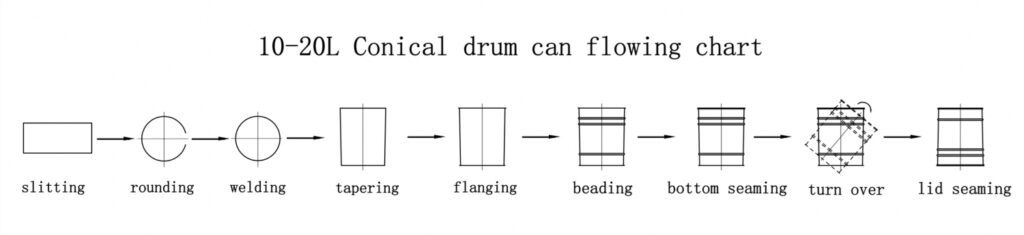
4. ADVANTAGES AND DISADVANTAGES OF THE FULL-AUTOMATIC PRODUCTION LINE OFCONICAL PAIL
Advantages: the whole production line adopts automatic computer programming control system, fully realizing the full automatic assembly line work.Only 1-2 workers are needed to complete the operation of the entire production line.The whole production line has fast production speed, high production efficiency, automatic fault detection system and low rejection rate.
Disadvantages: compared to semi-automatic production line, the initial investment capital is larger. For the start-up enterprises,It is recommended to use semi-automatic production line with less capital in.
5.DELICACY PRODUCTS AND PEER PRODUCTS COMPARISON
Delicacy products: through professional design, the whole production line can achieve quick replacement of double seaming and triple seaming requirements, adjustable expanding rib mold, precise cooperation of imported guide rail and profile combined with servo motor, to ensure fast flow conveying system. Eight roller can sealing head and can sealing quality are stable and fast. At the same time, the sealing head is specially designed, which has the characteristics of low noise and high efficiency.
Products of the same industry: the whole production line can only achieve the production of double seaming or triple seaming. The expanding mould is fixed and can not be adjusted at will. Common profile and domestic track, combined with stepping motor coordination, lack of stability and accuracy. There are only four rollers in the head of the can sealer, so the quality and speed will have a certain impact. At the same time, the machine head adopts old-fashioned design, and the production noise is large.
6.APPLICATION INDUSTRY
This production line is applicable to the production of metal round cans for food, medicine, chemical industry, paint, cooking oil and other industries. It can also be used in the production of food cans, paint cans, edible oil cans, paint cans, milk powder cans, aerosol cans, etc.
7.APPLICABLE COUNTRIES AND REGIONS
Applicable to countries or regions where labor is difficult, unstable, or highly paid. For example: Malaysia, Indonesia, Philippines, Vietnam, Thailand, India, dubai and so on.
Applicable to countries or regions with high output and high product quality. For example: Saudi Arabia, dubai, Russia, Canada, South Korea, Turkey and so on..
8.WHY TO CHOOSE DELICACY PRODUCTS?
1. Established 20 years ago, Delicacy technology is a well-known brand in the Chinese industry.
2. More than 80% of customers in China have used Delicacy products.
3. Delicacy technology has a strong technical team and professional after-sales service to provide customers with turnkey project and one-stop service.
4. Once choosing Delicacy technology products, Yixin technology will provide you with the most professional technical advice and guidance from material selection, printing and typesetting, installation, commissioning to smooth production